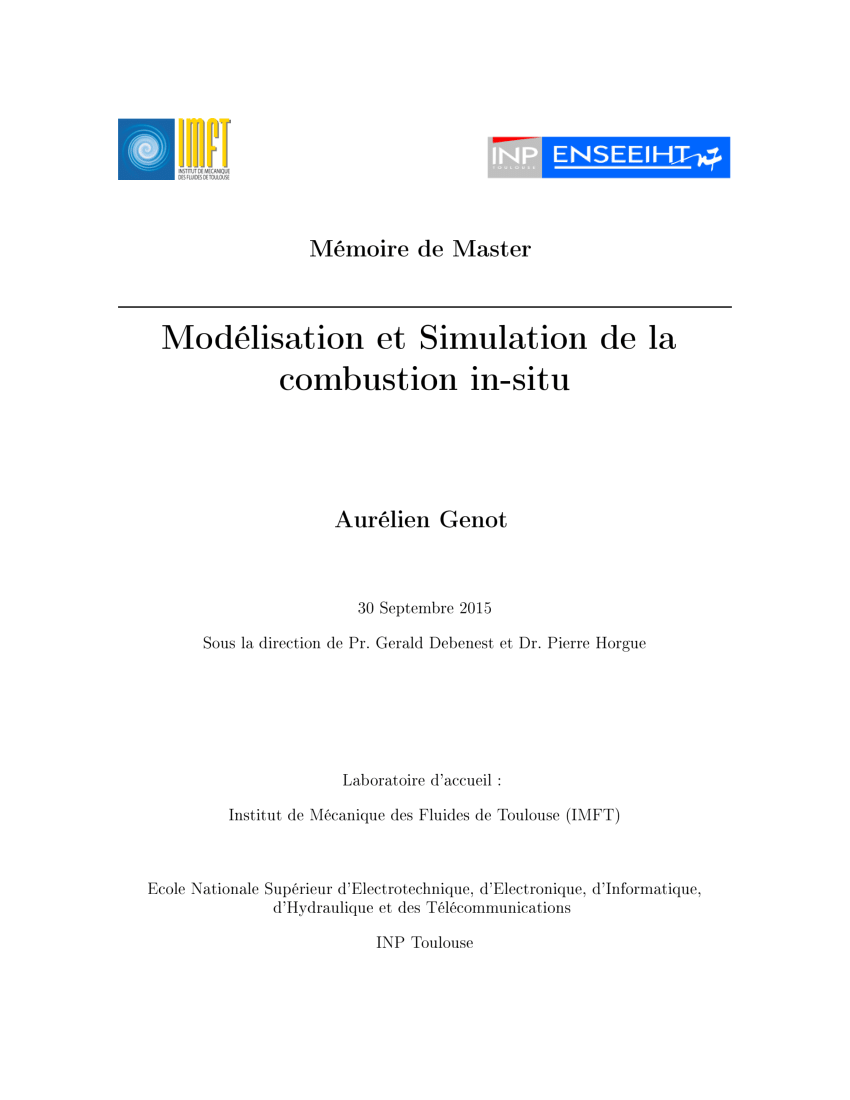
Master thesis: Plant simulation. Division Rock Tools, part of business area Sandvik Mining and Rock Solutions, offers a thesis project within the area of plant simulation. Business area Sandvik Mining and Rock Solutions is a leading supplier in equipment and tools, service and technical solutions for the mining and construction industries Master Thesis: Simulation of Air-cooled Edge Datacenter. The AI-net Aniara research project investigates how data centers in the future can be integrated with 5 / 6G infrastructure to support future IT services. In work package 5 "Infrastructure and power EDGE", RISE, Ericsson, Systemair, ELTEK and Enoc work with solutions within technical Degree Programme in Information Technology, Master’s Degree. Jani Hyvönen blogger.com Master’s Thesis. Simulation Aided Product Software Development. Supervisor Senior Lecturer, Software Engineering, blogger.com (Eng.), Jari Mikkolainen. Commissioned by Senior Manager, Member of the CEO Technology Council, PhD (Computing), Tero Rissa. Tampere
Master Thesis LTE Simulation Projects (Research Help)
edu no longer supports Internet Explorer. To browse Academia. edu and the wider internet faster and more securely, master thesis simulation, please take a few seconds to upgrade your browser. Log in with Facebook Log in with Google.
Remember me on this computer. Enter the email address you signed up with and we'll email you a reset link, master thesis simulation. Need an account? Click here to sign up. Download Free PDF, master thesis simulation. Master's Thesis: Modeling and Simulation of a Diesel Ship Propulsion Plant. Kamal Kharroubi. Download Download PDF Full PDF Package Download Full PDF Package This Paper. A short summary of this paper, master thesis simulation. The model was master thesis simulation with the aim of simulating the working of a large marine propulsion plant on the screen of a computer without recourse to the realization of each one of the components of the whole ship propulsion plant, master thesis simulation.
The large marine Diesel engine of the ship is modeled according to a semi-experimental modeling approach developed in a previous article by the same author. This approach is based on the simultaneous use of characteristic data of the components of the engine and real engine testing data sheets. This is motivated by the fact that the data necessary for the equations representing the phenomena happening inside a marine Diesel engine are not always available. Also, the modeling of the marine Diesel engine is based on the use of mathematical equations master thesis simulation on the use of relatively simple models of the engine governor, the engine torque limiter, and the auxiliary blower.
To the large marine Diesel engine model, propeller and ship models have been added and the model of the whole marine propulsion plant was built. The model was tested by the input of a speed schedule, of a staircase form, in which the master thesis simulation is sometimes constant and sometimes increasing linearly and the results were in a good agreement with test bench trials records of the large marine Diesel engine, when the model of this engine was solely tested, whereas no ship sea trials data were available for the evaluation of the results obtained when the model of the whole ship propulsion plant was tested.
Moreover, further research for finding the best mathematical models for each one of the components of this marine propulsion plant must be carried out. All in all, this thesis provided a first simplified master thesis simulation for the modeling and the simulation of a Diesel ship propulsion plant that is easy to comprehend and very straightforward to implement.
The large two stroke marine Diesel engine still remains one of the favorite choices of both ship owners and shipyards. The benefits of large diesel engines in marine propulsion are the superior efficiency, the possibility of burning heavy fuel oil and that slow-speed engines can be directly connected to the propeller without the need of a gearbox and clutch. The accuracy of these predictions will depend on the models used to model the engine for the simulation.
In more details, the cost involved in purchase and installment of a two-stroke marine diesel engine is high. Moreover, the sheer physical size and power output of the largest engines makes it difficult and time consuming setting up a proper test bed facility.
Therefore the use of engine models to describe the engine behavior is essential to understanding how different parameters affect the system, and to be used in controller design and testing. Consequently, the use of simulation for transient response and optimization is of utmost importance. The ship propulsion system is a very complex and delicate system and its behavior depends on the interactions between its different master thesis simulation which are the marine Diesel master thesis simulation, the turbocharger, the marine propeller and the ship.
Gaining access to the knowledge of the influence, that could bring a change in the characteristics of every one of master thesis simulation elements of the marine propulsion plant, on its response will lead to a better understanding of the working of the whole propulsion plant and will be of great help during the design process.
Obviously, one cannot build a real marine propulsion plant and start changing every one of its elements to test the influence of the characteristics of each element on the behavior of the whole installation, a much more realistic and affordable approach will be based on the simulation of the working of master thesis simulation ship propulsion plant on the screen of a computer. The ultimate goal is to build a simulation model that can predict, master thesis simulation acceptable accuracy, the response of the marine propulsion plant and can allow for further testing of the plant by changing the characteristics of each one of its components.
In this article a semi- experimental modeling approach for the simulation of a large marine engine is presented. The engine, which is of the two stroke marine Diesel type, is modeled by means of a cycle mean value model. According to that, two nonlinear first order differential equations, which are derived by applying master thesis simulation angular momentum conservation in engine crankshaft and turbocharger shaft, are used for the master thesis simulation of engine crankshaft and turbocharger shaft rotational speeds.
The other engine operating parameters are calculated after the solution of a non-linear algebraic system of three equations corresponding to the mass and energy balances in the engine components. The problem with the already existing models is that they are involving, master thesis simulation, air cooler characteristics, engine characteristics, master thesis simulation, and exhaust piping system characteristics which are not always available.
So in order to solve this problem, the data recorded in the engine testing data sheet of the engine to be simulated, and relative, to the pressure difference in the air cooler, to the temperatures of the air exiting the compressor and the air entering the engine, to the specific fuel oil consumption, and to the pressure of the exhaust gas at the outlet of the turbocharger, is exploited.
This data is taken and the Curve Fitting Toolbox included in MATLAB is used to fit the following four curves: the curve of the variation of the pressure drop in the air cooler as a function of the fuel rack position, the curve of master thesis simulation variation of the air cooler effectiveness as a function of the fuel rack position, the curve of the variation of the mass of injected fuel per cylinder and per cycle as a function of the fuel rack position, and the curve of the variation of the pressure increase in the exhaust piping system of the turbocharger as a function of the fuel rack position.
The four new models, obtained this way, are composed of quadratic and cubic polynomials and are used in this modeling approach. The mathematical equations of the marine engine model are implemented and solved using the computational environment MATLAB Simulink ®. Then, the simulation, master thesis simulation, under various operating conditions of the large marine engine of which engine testing data sheet has been used in the modeling phase, is performed and the derived results are presented together with the experimental results available from test bench trials of the same engine.
In this part, the problem encountered during the modeling process is discussed, then the objective of the thesis and the proposed solution of the problem is stated. It is containing mainly the following three parts: Background and Motivation, Previous Work and Research Objectives, and Thesis Outlines. Also in this part, engine accessories like the engine governor, the torque limiter and the auxiliary blower are represented by models.
In this part all the models of the marine engine, master thesis simulation, developed in the second part, are implemented and solved. The results are represented together with the experimental results taken from the engine test bench trials records of the simulated engine. In this part the differential equation for the calculation of the longitudinal ship velocity is dissected and the different parameters involved in this equation are modeled or replaced by real values describing the characteristics of the ship chosen, master thesis simulation.
In this part all the additional models, developed in the fourth part, are implemented and solved using a computational environment. The representation of real master thesis simulation processes is enhanced as the complexity of the master thesis simulation simulation tool is increased but, at the same time, a greater amount of input data is required, the model execution time lasts longer, and the model usage becomes more laborious.
In the following, master thesis simulation, three definitions of the mean value engine models MVEMschosen from the available literature, are cited. In reference [1], the authors said that the essence of the mean value engine modeling is to capture a certain dynamic behavior of the physical system to a certain degree of approximation on the time scales of several engine events.
In reference [2], the authors stated that MVEMs seek to predict the mean values of the gross external engine variables for example crank shaft speed and manifold pressure and the gross internal engine variables for example thermal and volumetric efficiency dynamically in time.
The time scale of this description is much longer than a single engine cycle and much shorter than the time required for a cold engine to warm up cycles master thesis simulation so. In reference [3], it is explained that the MVEMs are simplified dynamic engine models based on engine physics and involve averages rather than instantaneous values of the engine variables. Engine variables such master thesis simulation the mass air flow rate, the manifold air pressure, master thesis simulation, and the manifold air temperature evolve quasi periodically over the engine cycles through different dynamic modes which essentially depend on the crank angle.
These dynamic modes arise due to opening and closing of intake and exhaust valves during different stokes of the engine, namely intake, master thesis simulation, compression, expansion and exhaust strokes. The MVEMs do not consider these different modes in each cycle or the pulsating instantaneous flow which exists in reality. Rather, it describes the evolution of engine variables averaged over engine cycles in terms of a single dynamic mode essentially by considering average air flow into the cylinder.
MVEMs have master thesis simulation widely used to examine the engine dynamic behavior and to master thesis simulation and test engine control schemes, because of their ability to represent the engine behavior with sufficient accuracy, while requiring limited amount of input data and quite a reasonable time of execution.
However, the modeler must be aware of the limitations of these MVEMs, which are associated with the simplification of the geometry, the time scale, and the oversimplification of the physical phenomena involved. Some of the most troubling issues in master thesis simulation modeling through MVEMs can be found in [4], and different approaches to modeling turbocharged diesel engines, in the mean value sense, are presented in [5].
The marine engine is modeled by considering the phenomena occurring in its components. The engine components taken into consideration are the engine cylinders, which are placed between the engine inlet receiver and the engine exhaust receiver, the engine turbocharger, which is composed of the compressor and the turbine connected in a single shaft, and the engine air cooler, which comes immediately after the compressor with the task of cooling the hot air delivered by the compressor.
As far as two stroke marine diesel engines are concerned, the flow of air through the turbocharger compressor is modeled as an adiabatic compression process. The compressor ensures the required air mass flow rate in order to sustain the perfect combustion regime in the combustion chambers. The air mass flow rate is considered in quasi- steady engine models to be continuous. Restriction of air flow is imposed due to the presence of inlet ports and exhaust valves, which induce interruptions to continuous air flow.
From the engine testing data it has been found that the condition b is satisfied and consequently the equation has been used.
S is the stroke of the engine in meters. Consequently a PID engine governor model has been chosen for the generation of the fuel rack position commanding the engine. The engine governor model is shown in Fig. Its master thesis simulation function is to limit the master thesis simulation rack position, ordered by the engine governor, to a preset value depending on the engine speed.
So in order to remedy this problem an auxiliary blower block has been added to the model, master thesis simulation. The design of this block is based on the idea that an auxiliary blower has a pressure contribution, which is added to the pressure in the inlet receiver, master thesis simulation, and an air mass flow rate contribution, which is added to the air mass flow rate flowing into the engine.
In the case studied, the auxiliary blower is on when the engine speed is between 0 and Only an air mass flow contribution equal to So due to the absence, in the literature, master thesis simulation, of information about the value of the pressure contribution of auxiliary blowers and about the effect of this pressure on the overall pressure in the sizeable scavenge air receiver, master thesis simulation value of zero has been given to the pressure contribution of the auxiliary blower in this case.
The auxiliary blower model is depicted in fig. The rest of the parameters involved in equations 2the exhaust receiver pressure,and the exhaust receiver 4 and will be found by using equations 68911121314 master thesis simulation, 151617 and For the calculation of the engine shaft speed, necessary for the calculation in equations 16 and master thesis simulationand of the turbocharger shaft speed, used in the compressor performance map to find the compressor pressure ratioequations 19 and 20 are used, and the parameters required for the calculation procedure in these two equations are found by using equations 21222324252627 and The marine engine model consists of the following types of blocks: a the PID governor block, b the torque limiter block, c the turbocharger, air cooler and inlet receiver block, d the auxiliary blower block, e the block for the calculation of the mass of injected fuel per cylinder and per cycle, f the block for the calculation of the fuel mass flow rate, g the block for the calculation of the proportion of chemical energy of the fuel contained in the exhaust gas and of the brake mean effective pressure, h the block for the calculation of the coefficients of the system formed by the equations 24 andi the block for the calculation of the air mass flow rate and of the exhaust receiver pressure and temperature, j the block for the recalculation of the exhaust receiver pressure, k the block for the calculation of the turbocharger speed, l the block for the calculation of the engine speed, m the block for the calculation of the engine brake power.
This engine is of the two-stroke marine Diesel type, turbocharged by the Mitsubishi Heavy Industries MET83SE turbocharger. Also it is assumed that this engine is directly connected to a ship type propeller via the shafting system which means that the gearbox is not installed. The engine main characteristics are given in table 3. Table 3. The simulation is controlled by a speed schedule, of a staircase form, in which the speed is sometimes constant and sometimes increasing linearly, the starting speed in this speed schedule is Each speed remains constant for a period not less than s before increasing linearly to the next speed.
Generally, almost all the operating parameters of the engine are following the form of the speed schedule, in their variation, from the beginning of the period of the simulation until its end.
However, there master thesis simulation some happening phenomena which must be master thesis simulation. During the first 50 s of the simulation time the speed of the engine is fluctuating slightly around After the th s, the speed of the engine starts exceeding Consequently, master thesis simulation, around the th s, there is a drop in the exhaust gas pressure and temperature which leads to a fall in the speed of the turbocharger.
The graph of the variation of the scavenge air temperature is not following the form of the speed schedule until after the th s, before that it is almost an horizontal line with a fall during the first 50 s and a sharp increase between the th s and the th s.
From the fuel index master thesis simulation the engine states are calculated. The propeller uses the speed of revolution from the engine n to calculate the load torque Qp. This is found from the ship velocity Vs, master thesis simulation. The propeller load torque is then used to recalculate the engine speed, and the propeller thrust to decide a new ship speed.
writing a master's thesis - my experience
, time: 14:15Matlab Simulation Master Thesis (Research Assistance)
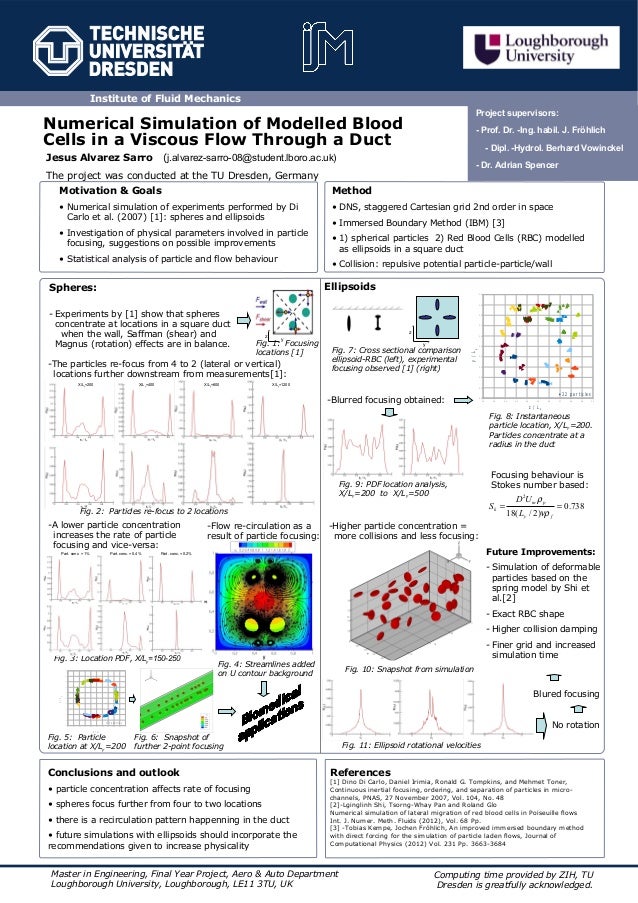
Master Thesis: Simulation of Air-cooled Edge Datacenter. The AI-net Aniara research project investigates how data centers in the future can be integrated with 5 / 6G infrastructure to support future IT services. In work package 5 "Infrastructure and power EDGE", RISE, Ericsson, Systemair, ELTEK and Enoc work with solutions within technical In this thesis a model of a Diesel ship propulsion plant containing a large marine Diesel engine, a turbocharger, a propeller, and a large container ship was built. The model was constructed with the aim of simulating the working of a large marineEstimated Reading Time: 17 mins Master Theses in Development of Simulation, Optimization and Compiler Tools Introduction Simulation and optimization of dynamic systems is becoming a standard tool in several industrial branches. This trend is largely driven by the need to decrease product time-to-market. In order to increase productivity in the product design
No comments:
Post a Comment